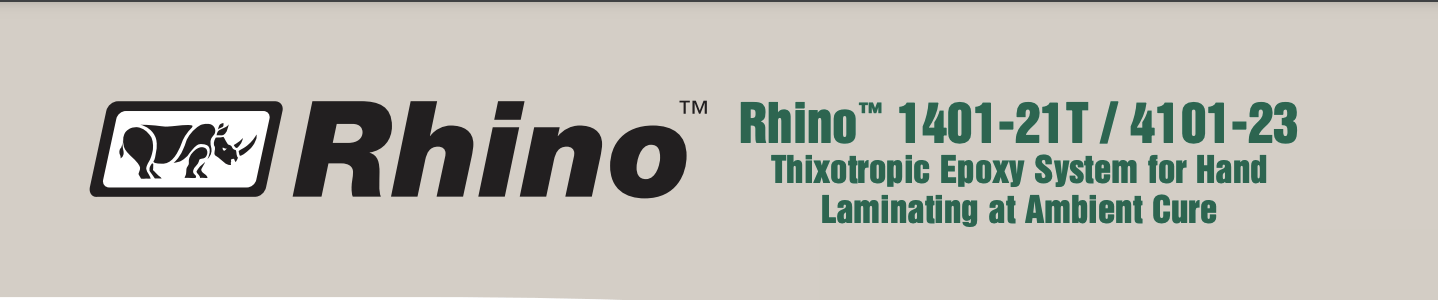
DESCRIPTION
Multifunctional epoxy and cycloaliphatic-amine blend hardener for high performance composite parts. One hour pot life, with fast cure development at typical ambient temperatures. Thixotropic resin will not drain from laminate.
Excellent combination that provides good thermal resistance, excellent fatigue and interlaminar shear strength with rapid wetting of E-glass fiber reinforcements. Rhino Linings 1401-21T Epoxy Resin is formulated for highly increased E-glass fiber compatibility. Low toxicity, low odor system. No VOCs, 100% solids.
SUGGESTED USES
Hand lay-up of composite fiberglass reinforced structures.
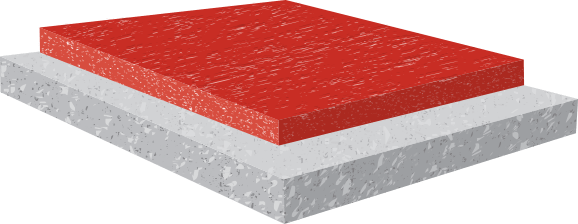