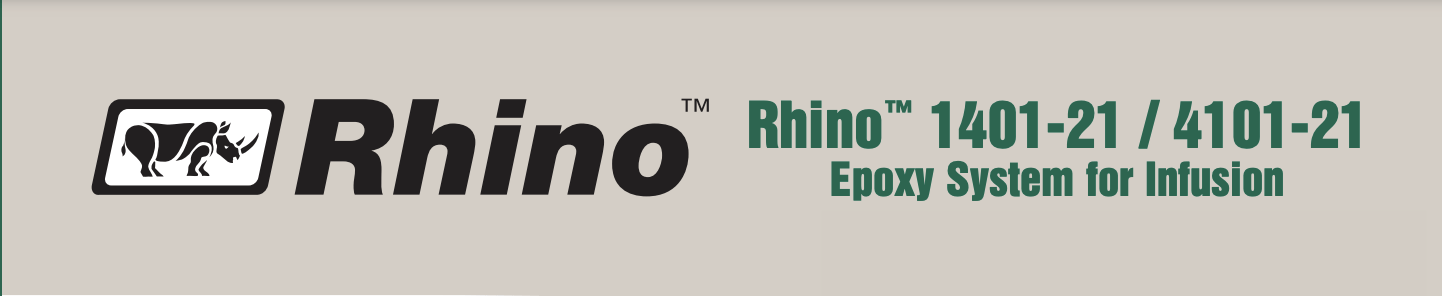
DESCRIPTION
Multifunctional epoxy and cycloaliphatic-amine based hardener for producing high performance composite parts. Two curing agents (4101-21 fast and 4101-21 slow) provide a complete range of working times from 30 minutes to 6 hours, and by blending the curing agents, any point in between.
Rhino 1401-21 with 4101-21 provides for ample pot life with fast cure development at standard molding temperatures. Rhino 1401-21 provides good thermal resistance, excellent fatigue and inter-laminar shear strength with rapid wetting of fiber reinforcements. Rhino 1401-21 Epoxy Resin is formulated for highly increased E-glass fiber compatibility. Low toxicity, low odor system, no VOCs, 100% solids.
SUGGESTED USES
- Resin infused composite rotor blades
- Large fiberglass reinforced structures
- CIPP applications
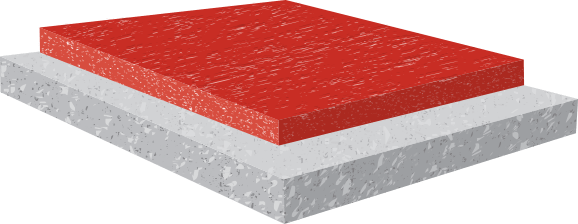