
DESCRIPTION
Rhino™ 102HT is a toughened, high temperature use structural epoxy adhesive designed for the bonding of fiberglass to itself and many dissimilar materials. It is a two phase (toughened) epoxy resin produced using a CTBN elastomer with a flexible epoxy resin backbone for maximum stress and fatigue resistance. 102HT bonds with an immediate high tack consistency, and offers a quick cure when used at ambient temperatures ranging from 60°F (15°C) to 95°F (35°C). The working life at 77°F (25°C) is 60 minutes (working time increases with lower ambient temperatures), with full cures occurring between 12 – 14 hours depending on cure temperature.
Unlike most epoxy adhesives, 102HT adhesive cured at ambient temperatures provides heat resistance well in excess of most engineering limits with an HDT of 105º C (220°F ). The material mixes at 100:35 by weight (resin to hardener). The convenient color-coded components form a uniform color when properly mixed. Rhino 102HT adhesive is designed for high production meter/mix ram dispensing and although highly thixotropic, it offers very fast application rates. 102HT adhesive is solvent free, and 100% solids.
SUGGESTED USES
Use Rhino 102HT adhesive to bond fiberglass to itself, and other materials such as concrete, metal, wood, and many plastics. Rhino 102HT adhesive is highly recommended as a “tack coat” for applying epoxy resin saturated reinforcement materials to vertical and overhead substrate such as concrete, or steel in the areas of seismic retrofit and structural upgrades.
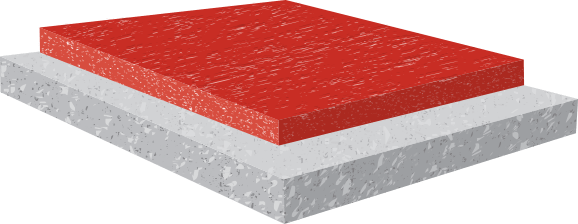