
DESCRIPTION
Rhino™ 9700 Novolac is a high quality Bis-F epoxy novolac coating and lining system which has superior chemical and abrasion resistance versus Bis-A type epoxy resins. This tightly crosslinked epoxy system cures in the presence of moisture and humidity with excellent mechanical properties.
Rhino 9700 mixes using the industry standard, 2:1 by volume ratio. Having low odor, Rhino 9700 contains no solvents and is 100% solids that assures ease of application. Rhino 9700 Novolac viscosity is well suited for vertical applications.
FEATURES & BENEFITS
- Well suited for vertical applications
- Superior chemical and abrasion resistance
- Excellent bonding
- Highly resistant to cratering or blush
- Dries to a high gloss
- Low odor
- 100% solids, no solvents
- Cures in the presence of moisture and humidity with excellent mechanical properties
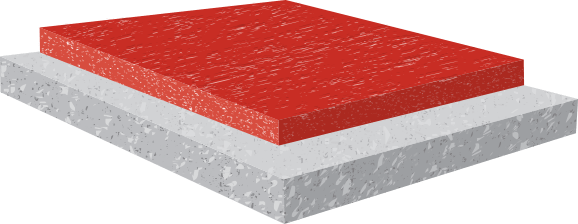