DESCRIPTION
A
Abrasion Resistance:
Ability of a coating to resist degradation due to mechanical wear by hard and rough objects (mechanical erosion) thanks to the ability to dissipate the applied mechanical energy.
Aliphatic:
An aliphatic compound is one that is not aromatic; i.e. it lacks a particular arrangement of atoms in its molecular structure.
Adhesion:
Degree of attachment between a coating film and the underlying material to which it is in contact. The two surfaces are held together by interfacial forces which may consist of valence forces or interlocking action.
Ambient Temperature:
Room temperature or the existing temperature of the surroundings.
Amide Resin:
Organic compound that contains a carbonyl group bound to nitrogen. -CON- (C double bonded to O)
Amino Resin:
Thermosetting resin manufactured from amino compound and formaldehyde. Amino resins are often used as curing agents for epoxy coatings
Aromatic:
An aromatic molecule or compound is one that has special stability and properties due to a closed loop of electrons.
B
Bonding |
Attachment between a coating film and the surface to which it is applied. |
Bridging |
Formation of a coating film over a depression. |
C
Catalyst: |
Substance whose presence increases the rate of a chemical reaction, e.g., acid catalyst added to an epoxy resin system to accelerate drying time. |
Cast, Casting: |
The filling of essentially open molds with liquid mixtures of polyurethane reactants or liquid monomers and allowing them to polymerize. A CPU is a cast polyurethane. |
Clear Coating: |
A transparent protective and/or decorative film; generally the final coat of sealer applied to automotive finishes. |
Chalking: |
Coating defect: formation of a powdery surface condition due to the disintegration of the surface binder or elastomer caused by weathering, fuel, or other destructive environmental factors (exposure to ultraviolet radiation). Results on a loss of gloss. |
Chemical Resistance: |
Coating’s resistance to solvents, acids, and alkali testing done under watch glass for 24 hours. |
Coat: |
The lining/coating applied to a surface in a single application to form a film when dry. |
Coating: |
Liquid, liquifiable or mastic composition that is converted to a solid protective, decorative or functional adherent film after application as a thin layer. |
Coating Thickness: |
A coating is applied at a dry film thickness (DFT) of up to 20 mils (0.02 inches / 20/1000 of an inch / 1/50 of an inch). See Lining Thickness: (20+ mils DFT) |
Colorfast: |
Non-fading in prolonged exposure to light. |
Color retention |
Ability of a coating/lining to retain its original color during weathering or chemical exposure. |
Color Retention: The ability of a coating/lining or lining to keep its original color. Major threats to color retention are exposure to ultraviolet radiation and abrasion by weather or repeated cleaning. |
Compatibility: |
Ability of two or more coating components to mix with each other in a wet or dry state to form a homogeneous composition without specific interactions. Compatibility of the binder with other components (additives, other resins, solvents etc.) is considered a major principle for formulating stable, quality paints. |
Component |
When applied to polyurethane manufacture, a component is one of at least two reactive materials that are mixed together to form a polymer. |
Corrosion |
The decay, oxidation or deterioration of a substance (steel, concrete and others) due to interaction with the environment. |
Crosslinking |
Formation of chemical bonds between polymer chains leading to the formation of a three dimensional network. This kind of process has the effect of producing gel in a thermoplastic polymer or converting it into a thermoset polymer. |
Cure |
Process by which a coating/lining is converted from a liquid to a solid. |
D
Dew Point: |
The temperature of a surface at a given ambient temperature and relative humidity at which condensation of moisture will occur. |
Dry Film Build: |
Amount of thickness produced in an application. Millimeters (mils) of dry film per mils of applied wet film. |
Dry Film Thickness (DFT): |
Depth or thickness of the dry coating in millimeters. Coatings when applied before drying are measured in wet mils. To determine the dry mil of actual remaining product, the solids content and rate of coverage must be known to estimate the dry mils. A mil gauge is commonly used on the job site to measure wet mils during application to adjust the spread rate for proper film build. Wet mils are always measured at 100% solids on the chart. |
Dry Time: |
Time needed for an applied coating/lining film to reach a set stage of cure or hardness. |
Dry to Tack Free: |
Stage at which a coating film will form a skin to which dust will not adhere. |
Dry to Touch: |
State of dry at which a coating film will not transfer onto an item lightly touched against it. |
Dry to Handle: |
Degree of cure at which a film will resist deformation due to handling. |
Dry to Recoat: |
Time required for a cured film to dry prior to the application of a second coat. |
E
Elastic: |
Ability of materials to recover their original size, shape and volume after deformation. |
Elastomer: |
A synthetic rubber-like material capable of rapid, reversible extension. |
Epoxy Resin: |
Synthetic resin characterized by the presence of the epoxy group, derived from petroleum products that can be cured by a catalyst or used to upgrade other synthetic resins to form a harder, more chemically resistant film. This resin possesses high mechanical strength, good adhesion, and resistance to solvents, acids, alkali, and corrosion. |
F
Filler: |
An inert material added to a polyurethane reaction mixture. Fillers are usually solid, particulate materials such as glass or silica. |
Fire Resistance: |
The ability of a coating to withstand fire or to protect the substrate to which it is applied from fire damage. |
Fire Retardant: |
A coating which will (1) reduce flame spread, (2) resist ignition when exposed to high temperature or (3) insulate the substrate and delay damage to the substrate. |
Flammable: |
Substance easily ignited in the presence of a flame; any liquid having a flash point below 100°F (37.8°C). |
Flexibility: |
Degree at which a coating is able to conform, to movement or deformation of its supporting surface without cracking or flaking. |
G
Gelled: |
Coating/lining which has thickened to a jelly like consistency, making it unusable. |
Gloss: |
Sheen or ability of a surface to reflect light. Gloss is measured at a 60° angle. |
Gloss Retention: |
Ability of a coating/lining application to retain the original sheen during weathering |
H
Hard Dry: |
Full cure of a coating: usually 72 hours to 5 days. |
Hardener: |
Curing agent for epoxies or fiberglass. |
High Build: |
Coating which can produce a thick film in a single coat. |
I
Impact Resistance: |
Ability of a coating to resist deformation or cracking due to a forceful blow. |
Isocyanate: |
A substance containing an isocyanate (-N-C-O) group. A polyisocyanate contains more than one isocyanate group. |
M
Mil: |
A unit of measurement in the English system that is measured in thousandths of an inch. (.001 = one thousandth of an inch or 1.0 mil) |
Mil or mil thickness is the common measurement of a coating. One mil equals 1/1000 of an inch. A 1/4″ coating equals 250 mils. Coatings when applied before drying are measured in wet mils. To determine the dry mil of actual remaining product, the solids content and rate of coverage must be known to estimate the dry mils. A mil gauge is commonly used on the job site to measure wet mils during application to adjust the spread rate for proper film build. Wet mils are always measured at 100% solids on the chart. |
Unit used to measure coating thickness |
1/64 inch = 15.625 mils |
1/50 inch = 20 mils |
1/32 inch = 31.25 mils |
1/16 inch = 62.5 mils |
1/8 inch = 125 mils |
1/4 inch = 250 mils |
1/2 inch = 500 mils |
3/4 inch = 750 mils |
1 inch = 1000 mils |
Matting: |
Reduction of the gloss of a coating at a given angle due to the effect of diffuse light scattering by the coating surface. Matting is affected by the surface topography, pigmentation, and specific matting agents. |
Matting Agent: |
Additive used to reduce the gloss. |
Monomer: |
A substance that is capable of conversion into a polymer |
N
Nonflammable: |
Compound which does not burn in the presence of a flame. |
P
Paint: |
A coating/lining including resin, a solvent, additives, pigments and, in some products, a diluent. Paints are generally opaque, and commonly represent the portion of the industry known as “architectural coatings.” |
Peeling: |
Paint or coating/lining lifting from the surface due to poor adhesion. |
Percent Solids: |
Percentage mass of non-liquid components in paint. |
Polyaspartic: |
The name polyaspartics has recently become popular among formulators in the industry due to the need to differentiate it from polyureas and polyurethanes. By definition, a polyaspartic is an aliphatic polyurea because it is the reaction of an aliphatic polyisocyanate with a polyaspartic ester – which is an aliphatic diamine. However, polyaspartic coatings are very different in both application and coating performance properties from conventional polyureas. Polyaspartic technology is closer in its applications and performance characteristics to 2-component aliphatic polyurethane coatings. |
Polyether: |
A polymer containing ether linkages. The polyethers used in polyurethane technology contain reactive hydroxyl end groups. |
Polymer: |
A high molecular weight substance, natural or synthetic, which can be represented as a repeated small unit (monomer). |
Polyol: |
A substance containing several hydroxyl groups. A diol, triol and tetrol contain two, three and four hydroxyl groups respectively. |
Polyurethane: |
Polymer made by the reaction of polyols with a multi-functional isocyanate. Provides toughness, flexibility, weather resistance, chemical resistance, and abrasion resistance to the coating film. |
Prepolymer: |
A polyurethane reaction intermediate made by reacting isocyanate with a polyester or polyether in which one component is in considerable excess of the other. |
Pot Life: |
Length of time a coating material is useable or sprayable after mixing. As mixed material reacts in the pot, the viscosity always increases. |
Primer: |
First complete coat of paint, coating or lining applied to a surface. Primers improve adhesion, corrosion resistance of the substrate, and increase compatibility with the topcoat |
R
Reaction: |
A chemical change in which two or more atoms or molecules give a new substance. |
Reflectance: |
Ratio of the intensity of reflected light to that of incidental light. |
Relative Humidity: |
Ratio of the quantity of water vapor present in the air to the greatest amount possible at a given temperature (expressed as a percent). |
Resin: |
Synthetic or natural material used as the binder in coatings. Can be translucent or transparent, solid or semi-solid. Examples: acrylic, alkyd, copal ester, epoxy, polyurethane, polyvinyl chloride, silicone. |
S
Sealer: |
Coating used on absorbent surfaces prior to a finish coat. |
Shelf Life: |
Period of time during which a paint stored according to the manufacturer’s instructions (packaging, temperature, humidity) retains its expected properties. |
Solids: |
The part of the coating that remains on a surface after the vehicle has evaporated. The dried paint/coating//lining film. Also called Nonvolatile. |
Solids by Volume: |
Percentage of the total volume occupied by nonvolatile compounds. |
Solids by Weight : |
Percentage of the total weight occupied by nonvolatile compounds. |
Solvent: |
Substance that dissolves other substances. Usually readily flammable volatile. |
Stabilizer: |
An additive that tends to keep a substance from changing its form or chemical nature. Stabilizers may protect against hydrolysis, oxidation, light, etc. (i.e. ultra-violet inhibitors). |
Structural Viscosity: |
See Thixotropy |
Substrate: |
Surface to be coated. |
Substrate: |
Any surface to which a coating/lining is applied. |
T
Tack Free: |
Completion of the initial cure process of a coating. Airborne dust and soil will no longer be trapped in the coating. |
Thixotropic Agent: |
Full bodied material that brings thixotropy to a paint/coating/lining formulation. |
Thixotropy: |
Property of certain materials to soften or liquefy upon agitation (viscosity decreases upon application of shear during brushing or roller), and to stiffen to its original state when allowed to rest (viscosity increases). A product that possesses thixotropy can resist the pull of gravity. |
Topcoat: |
Final coating/lining film applied to a surface. |
U
Urethane: |
An important resin in the coatings/linings industry. A true urethane coating is a two-component product that cures when an isocyanate (the catalyst) prompts a chemical reaction that unites the components. |
V
Viscosity: |
Measurement of a fluid’s resistance to flow. The common metric unit of absolute viscosity is the poise, which is defined as the force in dynes required to move a surface one square centimeter in area past a parallel surface at a speed of one centimeter per second, with the surfaces separated by a fluid film one centimeter thick. Since viscosity varies in inversely with temperature, its value is meaningless until the temperature at which it is determined is reported. |
V.O.C.: |
Volatile Organic Compound or liquid that is non-exempt. |
Volatile Organic Compound: |
Organic chemicals and petrochemicals that emit vapors while evaporating. In paints, VOC generally refers to the solvent portion of the paint which, when it evaporates, results in the formation of paint film on the substrate to which it was applied. |
Volatile: |
Amount of solvent or liquid components in a coating/lining. |
Volume Solids: |
Solid ingredients as a percentage of total ingredients. The volume of pigment plus binder divided by the total volume, expressed as a percent. High-volume solids mean a thicker dry film with improved durability. |
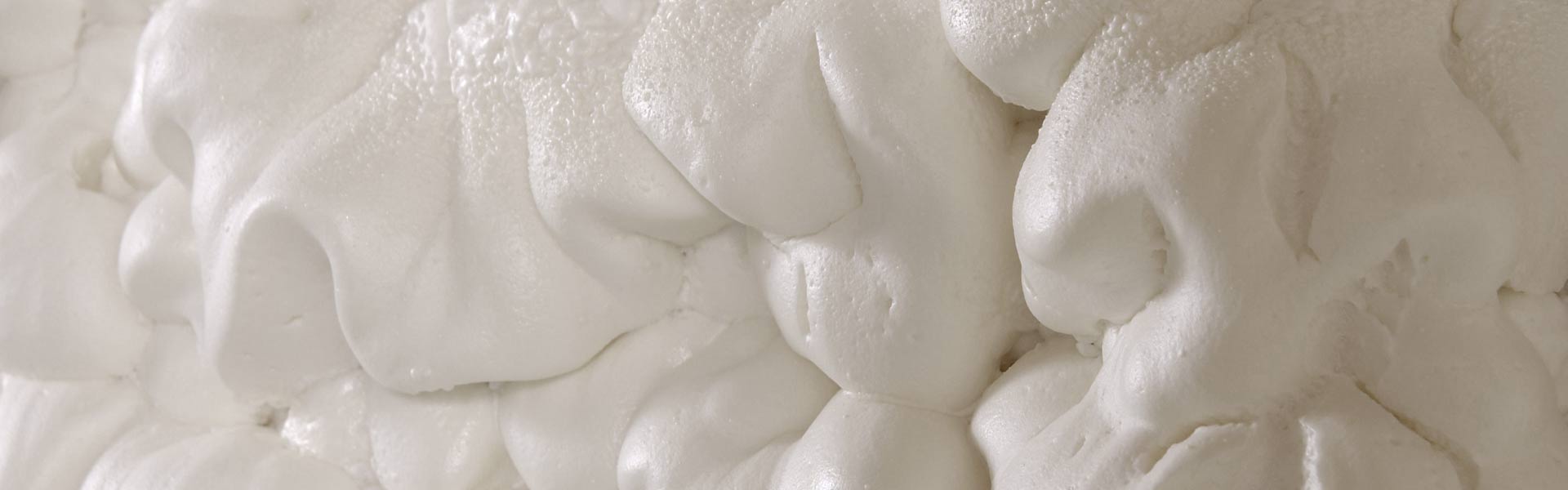
Open Cell Advantage
Interlocking air bubbles expand over 100 times their original size in about 4 seconds to create a soft, spongy, insulating barrier. Open cell spray foam insulation costs less per job and per R-value measurement allowing you to use much less material to cover more ground.
Open-Cell Content